What do you know about Flue Gas Analysis?
As per the
definition, flue gas (sometimes called exhaust gas or stack gas) is the gas
that emanates from combustion plants and which contains the reaction products
of fuel and combustion air and residual substances such as particulate matter
(dust), sulphur oxides, nitrogen oxides, and carbon monoxide.
When fuels
are burnt, certain combustion gases are produced; in industries, the gases of
combustion are called “heating gases.” After heating gases transfer their heat
to absorbing surfaces and are sent to the chimneys, they are called the “Flue
Gases.”
So, what do
we know about combustion?
Combustion
is the rapid oxidation of fuel that results in heat & light
As in, 1kg
(C3H8+C4H10) +O2 -> CO2+H2O+10900 Kcal
Stoichiometric
or ideal combustion:
When
available oxygen is just sufficient (neither more nor less) to convert all
carbon into CO2
As in, 2C4H10+13O2+3.76x13N2
-> 8CO2+10H20+3.76x13N2
Hence, our objective
is to come closer to stoich or ideal combustion
Flue gas
analysis is like a pathological test for humans that is preventive and used to
check the performance of the fuel we use for combustion. During the flue gas
analysis, we measure Oxygen, Excess Air, Carbon Monoxide, Carbon Dioxide, Oxides
of Nitrogen, Oxides of Sulphur, Ambient Temperature and Flue Gas Temperature.
Parameters |
Optimal Range |
Oxygen % |
2-6 |
Excess air % |
20-40 |
Carbon monoxide (PPM) |
<100 |
Carbon dioxide % |
<11 |
Oxides of Nitrogen (PPM) |
<100 |
Oxides of Sulphur (PPM) |
0 (nil) |
We conduct a flue gas analysis to detect the concentration of different gases and regulate the burner on a boiler to ensure optimal performance. Flue gas analysis is essential for evaluating air-to-fuel ratios in combustion for the best efficiency. Flue gas analysis is done by inserting a probe into the flue of a boiler, furnace, or other appliance between the last heat exchanger and draft diverter, or indeed any source of make-up air that may enter the flue that did not flow through the combustion process.
Here are the parameters SUPERGAS considers while performing flue gas analysis for the clients’ benefit:
Parameters |
Customer’s Advantage |
Measurement of Excess Air |
Very importantly, by adjusting excess air a little more than the stoich ratio, fuel consumption can be optimized. Too high & too low of excess air leads to fuel wastage. |
Free Oxygen |
Helps to adjust the air-fuel ratio in the burner in case the analysis shows higher free oxygen or too low oxygen. Saves fuel and costs. |
CO2, CO, SOx & Nox in Flue Gas |
Helps to monitor emissions for adhering to environmental norms. |
Flue Gas Temperature |
Helps to optimize heat loss, which saves on energy and costs. |
Call us on 9121177930 for flue gas analysis and seamless conversion from polluting fuels to effective and efficient LPG.
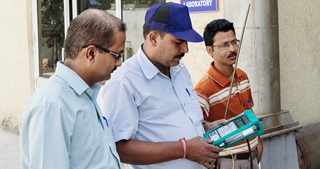