Maximize Cylinder Efficiency with Hydrotesting
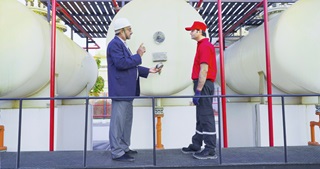
This essential testing method verifies the integrity and durability of cylinders, ensuring they can handle the pressures of daily use without compromise. Let’s explore the importance of hydro testing, the process involved, and the benefits it offers in safeguarding your operations.
About Hydrotesting
Hydrotesting is a
non-destructive testing method for determining the integrity of pressure
vessels, pipelines, and other equipment. This test also measures how thick the cylinder's outer layer is to make sure it hasn't gotten too thin from regular use over time.
Cylinders are made of materials that expand and contract with pressure changes, a feature critical for safety and efficiency. Factors like filling, handling, transportation, and contact surfaces can increase risks, potentially leading to LPG leakage and making the cylinder unfit for use. Here’s why Hydro testing is important:
Hydrotesting Procedure
Hydrostatic
testing involves filling a cylinder with water, pressurizing it in a test
jacket, and observing its expansion by measuring the displaced water. The
pressure used in this test is much higher than the pressure used during regular
use - usually, it's 50% more than the normal working pressure. If
the cylinder expands too much or differently when pressurized and afterwards,
it's considered unsafe and discarded.
When choosing the best industrial hydrostatic testing services, make sure:
SUPERGAS not only supplies LPG but also commits to the highest safety standards by continually enhancing our products, infrastructure, and skills to meet the growing market needs. Our Hydrostatic testing procedure is meticulously designed to ensure there are no leakages, thereby boosting safety and efficiency.
We take extra care to fill LPG to the precise quantity without any leaks, ensuring maximum efficiency for our customers. Furthermore, our commitment to quality is reinforced through periodic testing of cylinders and bullets, making certain that only the highest quality products are made available for our customers.
To know more about out safety standards and best practices while handling LPG in industries.